Polished concrete is one of the most durable and aesthetically pleasing flooring options on the market, but there is an option that may be even more appealing: adding dye to polished concrete. The dying process turns polished concrete floors into a true work of art, enhancing (not hiding) the natural characteristics of the concrete. Each dyed polished concrete floor is unique. So yes…virtually all structurally sound concrete floors, whether new or old, can be dyed and polished.
Adding color to the polishing process has become popular in offices, churches, educational, retail and commercial buildings. There are different products for coloring concrete including water-based dyes, solvent-based dyes, acid stains and water-based colorants. Although concrete stains and dyes seem to accomplish the same goal of adding color to the concrete, they can be very different in practice. So, the right choice will depend on the state of the concrete surface, location, as well as the desired end result.
Below are a few examples why we prefer water-based dyes:
- Environmentally friendly and safe for applicators
- Easier and more control when applying
- Perfect for polished concrete floors
- Stain colors will not peel or flake
- Safe to use in occupied spaces
- Adds color and depth to diamond- polished concrete
- No need to neutralize
- VOC-compliant
- Non-flammable
- Non-toxic
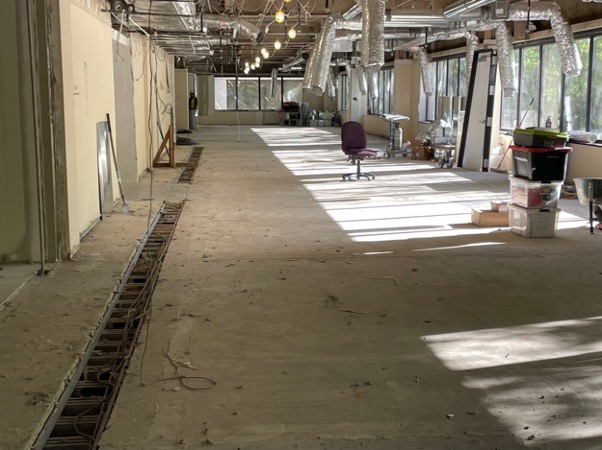
Case Study: Dyed polished concrete at an existing office building in Raleigh, North Carolina
Many factors are taken into consideration when building or remodeling an office building, from complying with regulations to creating a safe and attractive area for tenants and visitors. In these situations, it’s easy to overlook matters like flooring, but the type of flooring must be taken into consideration. While initial cost is a driving factor, maintenance costs should also be strongly considered. In worst case scenarios, fully operational businesses need to either stop or slow down operations to perform necessary maintenance.
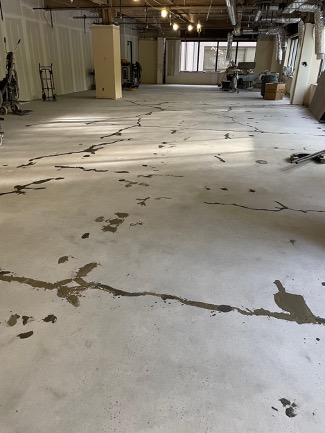
We recently had the opportunity to work with a reputable development and construction company at an office building in Raleigh, North Carolina. From our mock-up, we knew that polishing the existing concrete was going to present challenges that would require us to modify our normal procedures.
The floors being previously tiled and carpeted required us to remove any residue still on the concrete with our fist grind. We expected there to be areas of the concrete that would be soft as well as cracks, pits/voids and inconsistencies in the depth of the concrete.
We also knew that certain sections of the concrete had to be cut out and repoured to accommodate new plumbing pipes. This made it difficult for the ACC crew to do large sections at once. We decided to change our game plan and polish in sections up to 100- grit. Once the repoured sections were ready, the crew ensured that the new concrete and the existing concrete was smooth, even, and that all cracks and cuts were filled.
Because of the age of the concrete, a lot of patch work was needed. This step was necessary to fill cracks and pits/voids so the surface would be stronger, smoother, and, once polished, have a more attractive shine.
Concrete dye application
Depending on the results you want to achieve and the size of the job, dyes can be applied in a variety of ways. Most dyes are packaged in concentrated form, allowing flexibility in the end color. They can be used at full strength to attain greater depth of color or diluted with water or solvents to produce more translucent shades.
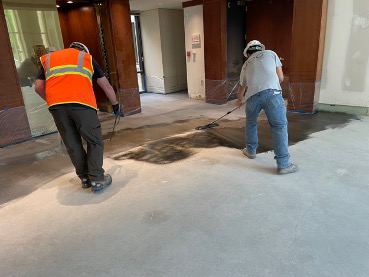
Regardless of the technique used, it is important to test the concrete surface for acceptance of the dye before application. The degree of penetration and intensity of color will vary depending on the application method used, age of the concrete, porosity of the concrete, cleanliness of the surface and other general conditions. No two dyed concrete surfaces will look exactly the same. A mock-up is used to verify a quality product prior to significant work being performed by the subcontractor. Mock-ups should be used to review unique details or materials to ensure they meet the desired design criteria and intent.
Due to the inconsistencies in the concrete from extensive patching and repours, certain areas of the floor did not want to accept the dye, but the ACC crew did a great job in making sure that the dye was consistent throughout through multiple dye applications. Although dyes are formulated to penetrate into the concrete, it is still necessary to protect dyed and stained surfaces from wear and contaminants by applying a guard/sealer.
Conclusion
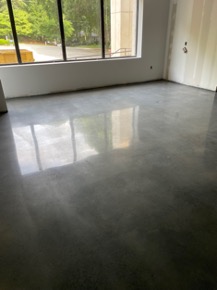
While polishing an existing concrete floor is more challenging than polishing freshly placed concrete, the concrete in this case was of high enough quality and it was properly prepared prior to dye application. By adding dye to the polishing process for this office building, a dynamically colored polished floor was created.